Zakończono wymianę pieców na wszystkich czterech instalacjach Clausa w Rafinerii Gdańskiej. W przeciwieństwie do swoich poprzedników, nowe aparaty zostały od początku zaprojektowane do utylizacji siarkowodoru przy użyciu powietrza wzbogaconego w tlen. Tym samym znacząco obniżyło się ryzyko ich awarii i jednocześnie poprawiło bezpieczeństwo pracowników. Jest to o tyle istotne, że w ciągu ostatniej dekady nominalna zdolność produkcyjna siarki zakładu w Gdańsku wzrosła o ponad 100 ton na dobę.
Najnowsza modernizacja instalacji Clausa – zrealizowana w latach 2020-2024 – to kolejny etap w doskonaleniu tego procesu i poprawy jego bezpieczeństwa. Poprzednie modyfikacje przeprowadzono w latach 2018-2019 w ramach Projektu EFRA, który spowodował istotny wzrost ilości wytwarzanego siarkowodoru. Przystosowano wtedy wszystkie cztery Clausy do pracy z użyciem powietrza wzbogaconego tlenem.
Normalna zawartość tlenu w powietrzu wynosi niespełna 21% (objętościowo). Instalacje Clausa w Rafinerii Gdańskiej mogą pracować z użyciem powietrza o zawartości tlenu do 28%, co uzyskuje się dodając do powietrza tlenu z wytwórni tlenu.
W procesie przerobu ropy naftowej siarka zawarta w ropie ulega w znacznej części konwersji do siarkowodoru, który jest usuwany na instalacjach głównie w procesie mycia aminowego, a następnie kierowany do instalacji Clausa w celu przekształcenia do czystej siarki.
– Przeznaczenie Clausów to utylizacja siarkowodoru – czyli tego związku, który powstaje podczas przerobu ropy naftowej na różnych instalacjach w rafinerii. Jest on absorbowany przez aminę i odparowywany w regeneratorze aminy, skąd kierowany jest do Clausów. Siarkowodór wydzielany jest również na instalacji stripera wód kwaśnych, do którego trafiają tzw. wody kwaśne z różnych instalacji rafineryjnych. Celem tej instalacji jest również usunięcie amoniaku. Oba związki trafiają na instalacje Clausa, gdzie następuje ich spalenie w powietrzu. Z siarkowodoru powstaje siarka, a gaz resztkowy trafia do instalacji doczyszczania gazu i jest spalany w dopalaczu – mówi Tomasz Bodnar, szef Zakładu Produkcji Wodoru i Siarki Rafinerii Gdańskiej.
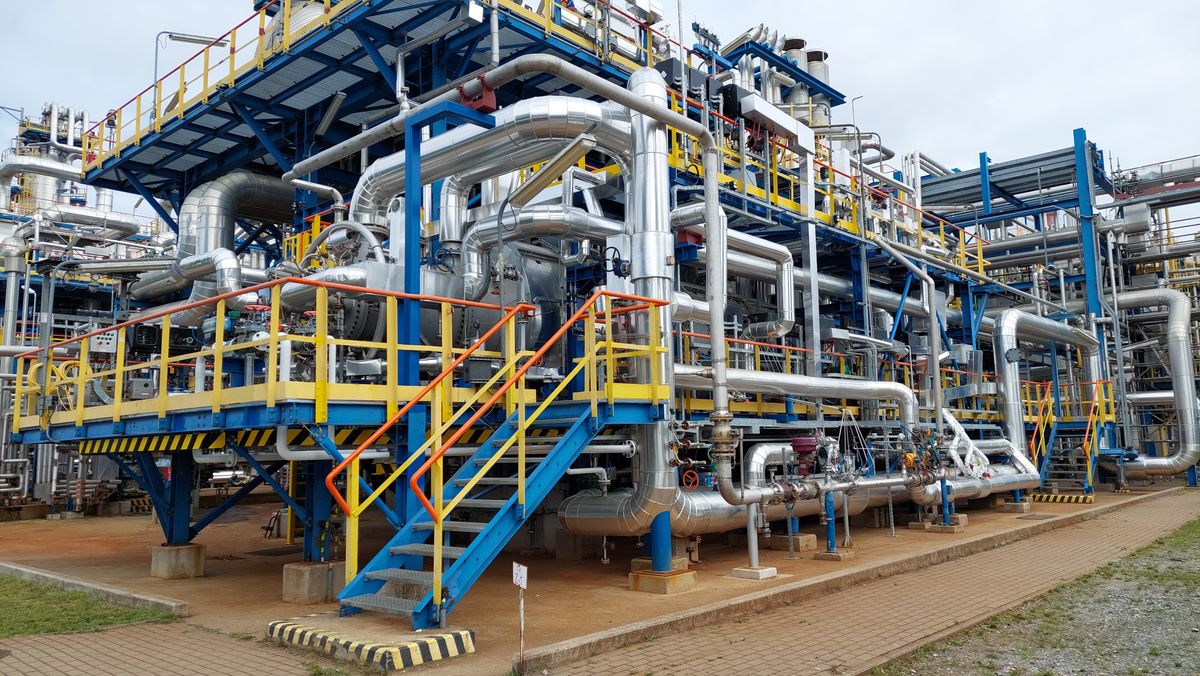
Znaczenie Clausów
Obecnie około 75% siarki zawartej w ropie przerabianej w Rafinerii Gdańskiej opuszcza zakład w postaci płynnej siarki elementarnej. Nie zawsze jednak tak było. Pokazuje to wykres „Produkcja siarki w Rafinerii Gdańskiej w latach 1991 – 2023”.
– Do 1999 roku tylko 10-15% siarki było usuwane z ropy, a pozostała część znajdowała się w produktach olejowych (napędowych, smarowych, opałowych) oraz w asfaltach. Wtedy do produkcji siarki w rafinerii wystarczała tylko jedna instalacja Clausa (tzw. osiemsetka – przyp. autor), o zdolności produkcyjnej 25 ton siarki na dobę. Zwiększanie przerobu ropy w rafinerii, a przede wszystkim pogłębianie przerobu – czyli zwiększanie produkcji paliw kosztem produktów ciężkich, głównie na instalacjach hydrokrakingu i koksowania – spowodowało znaczący wzrost zapotrzebowania na zdolności produkcyjne siarki – wyjaśnia Tomasz Bytner, szef Biura Koordynacji Produkcji Rafinerii Gdańskiej.
Pierwsze zwiększenie zdolności produkcyjnych siarki w gdańskim zakładzie nastąpiło w 1999 roku, kiedy na potrzeby pierwszego hydrokrakingu – instalacji 150 – wybudowano dwie nowe instalacje Clausa, 810 i 820, o łącznej zdolności produkcyjnej 120 ton siarki na dobę. Instalacja 800 została wtedy wyłączona z eksploatacji i zlikwidowana. Kolejne instalacje Clausa – 9810 i 9820 – wybudowane w ramach Programu 10+, uruchomiono w 2009 roku, zwiększając całkowitą zdolność produkcyjną siarki w rafinerii do 270 ton na dobę. Wzrost produkcji siarki wynikał z budowy drugiego hydrokrakingu oraz nowej instalacji hydroodsiarczania oleju napędowego.
W latach 2018 – 2019 – w ramach Projektu EFRA, który spowodował kolejny wzrost ilości wytwarzanego w rafinerii siarkowodoru, tym razem w związku z uruchomieniem instalacji koksowania (DCU, z ang. delayed coking unit) – zmodernizowano wszystkie cztery Clausy poprzez dodanie tlenu do powietrza używanego do spalania siarkowodoru. W ten sposób zwiększono zdolności produkcyjne Clausów do ponad 380 ton siarki na dobę. Specjalnie na potrzeby instalacji Clausa wybudowano w tamtym czasie także instalację produkcji tlenu wraz ze zbiornikami na ciekły tlen.
Aktualne zdolności produkcyjne siarki w Rafinerii Gdańskiej:
• dla instalacji 810/820 – po 72 t/dobę (łącznie 144 ton/dobę),
• dla instalacji 9810/9820 – po 119 t/dobę (łącznie 238 ton/dobę).
– Modernizacja istniejących już, dość wiekowych instalacji Clausa, które nie były pierwotnie przystosowane do pracy z powietrzem wzbogaconym tlenem, spowodowała znaczny wzrost wysilenia instalacji. Przede wszystkim wzrosły temperatury pracy. Zagrożenie potencjalnymi awariami było przesłanką do wdrożenia programu wymiany pieców na wszystkich Clausach. Chodziło o zamontowanie pieców od początku zaprojektowanych do pracy z powietrzem wzbogaconym w tlen – wyjaśnia Edmund Monkiewicz, emerytowany pracownik rafinerii w Gdańsku, obecnie ekspert w Biurze Dyrektora ds. Projektów i Rozwoju Rafinerii Gdańskiej.
– Problemem było przegrzewanie się płaszczy pieców. Doszło także do poważnej awarii pieca 9810, gdzie przepaliła się tzw. dennica (dolna spawana część kotła – przyp. autor). W rezultacie wprowadzono ograniczenia temperaturowe pracy tych aparatów: 1350°C w trybie normalnym, a 1400°C w trybie tlenowym, przy czym dla instalacji 9820 dopuszczono tylko tryb bez wzbogacania tlenem. Po wielu analizach i ekspertyzach, m.in. firmy Sulphur Experts, wobec stwierdzanego cięgle pogarszającego się stanu wymurówki, zdecydowano o wymianie pieców na tzw. OxyClausy, zaprojektowane przez firmę Air Liquide – dodaje Jan Kowalski, kierownik projektu w Biurze Realizacji Projektów Rafinerii Gdańskiej.
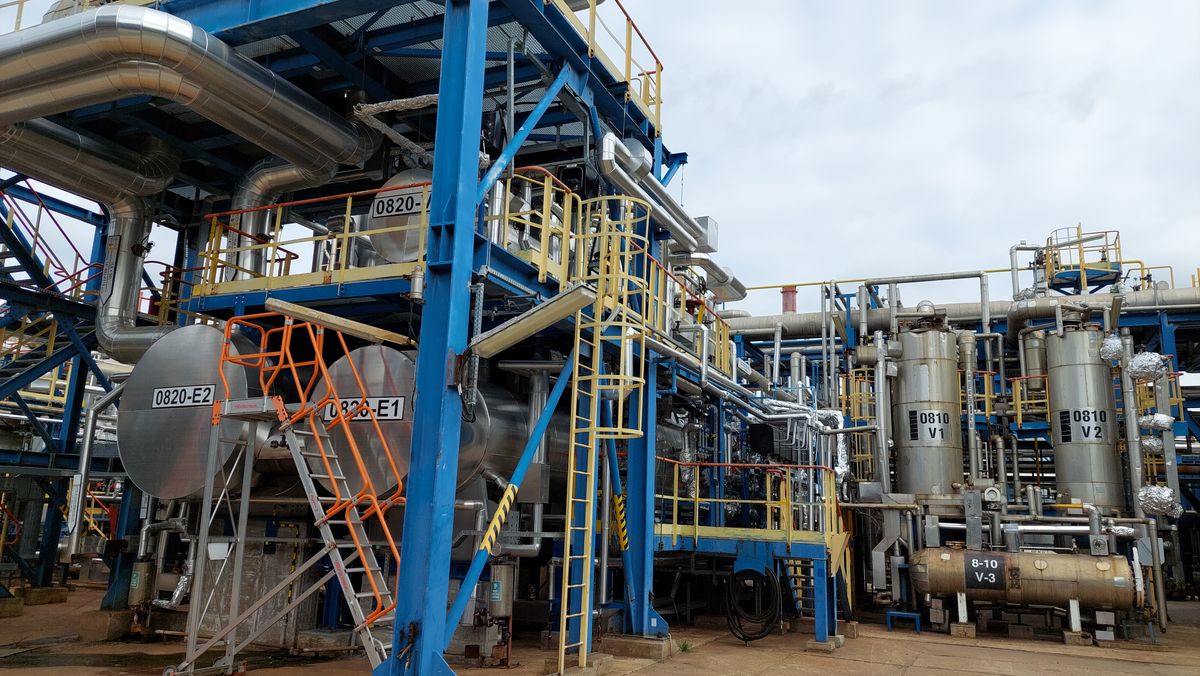
Jak przebiegała wymiana pieców
W 2020 roku rozpoczęto prace przygotowawcze do projektu i podpisano pierwsze umowy na dostawę aparatów, a następnie na wykonanie dokumentacji technicznej integracji nowych elementów z istniejącymi instalacjami. Dwa lata później podpisano umowę na realizację prac z ówczesnym LOTOS Serwis (obecnie ORLEN Serwis). Instalacje po wymianie aparatów uruchamiano odpowiednio w latach 2023-2024 (ostatnie uruchomienie odbyło się w 3. kwartale 2024 r.).
– Obecne rozwiązanie wydaje się technicznie bardzo korzystne. Widać to po pomiarach temperatur płaszczy pieców, co jest codziennie monitorowane przez kamery termowizyjne oraz pomiary ciągłe realizowane przez sieć termopar na płaszczach Clausów. Wykonujemy to, aby cały czas kontrolować czy nie ma wzrostu temperatury – tłumaczy Tomasz Bodnar. – Bardzo ważnym aspektem jest również poprawa bezpieczeństwa pracowników – kończy.
Dzięki odpowiednim szkoleniom, pomimo wielu wyzwań technicznych oraz istniejących zagrożeń, wszystkie etapy projektu odbyły się bez wypadków. Świadczy to nie tylko o profesjonalizmie zaangażowanych pracowników Rafinerii Gdańskiej i wykonawcy prac, czyli ORLEN Serwis, ale także o skuteczności stosowanych procedur bezpieczeństwa i dodatkowych inicjatyw BHP.
Kilka słów o procesie Clausa
Jest to proces produkcji elementarnej siarki z siarkowodoru (H2S), opatentowany przez niemieckiego chemika Carla Friedricha Clausa w 1883 roku. Metoda została zmodyfikowana przez niemiecką firmę IG Farben w 1938 roku i od tego czasu stała się standardowym procesem stosowanym do produkcji siarki,
a instalacje wykorzystujące ten proces nazywa się potocznie „Clausami”. Na świecie obecnie niemal cały siarkowodór oddzielany z gazu ziemnego oraz powstały w procesach przerobu ropy naftowej jest przekształcany do siarki w procesie Clausa. Ponad 90% siarki produkowanej na świecie uzyskuje się w takich instalacjach.
Rafineria Gdańska sp. z o.o. zarządza jednym z najnowocześniejszych zakładów produkcyjno-processingowych w tej części Europy. Jego moce przerobowe to ponad 10 mln ton ropy rocznie. Otrzymany surowiec przerabia się tu na wysokomarżowe produkty. Spółka zatrudnia obecnie ponad 1300 pracowników.
W listopadzie 2021 r., w wyniku reorganizacji ówczesnej Grupy Kapitałowej LOTOS, w jednym podmiocie zintegrowano całą działalność rafineryjną zlokalizowaną w Gdańsku. Wtedy to, ze spółki produkcyjno-handlowej (pod nazwą LOTOS Asfalt Sp. z o.o. funkcjonowała do 19 lipca 2022 r.) stała się podmiotem w pełni produkcyjnym.
Nowa struktura joint venture powstała w rezultacie procesu przejęcia kapitałowego Grupy LOTOS S.A. przez ORLEN S.A. oraz dołączenia jako wspólnika spółki Aramco Overseas Company B.V. z 30% udziałem w kapitale zakładowym.